Industries Served Aerospace and Industrial Coating Solutions
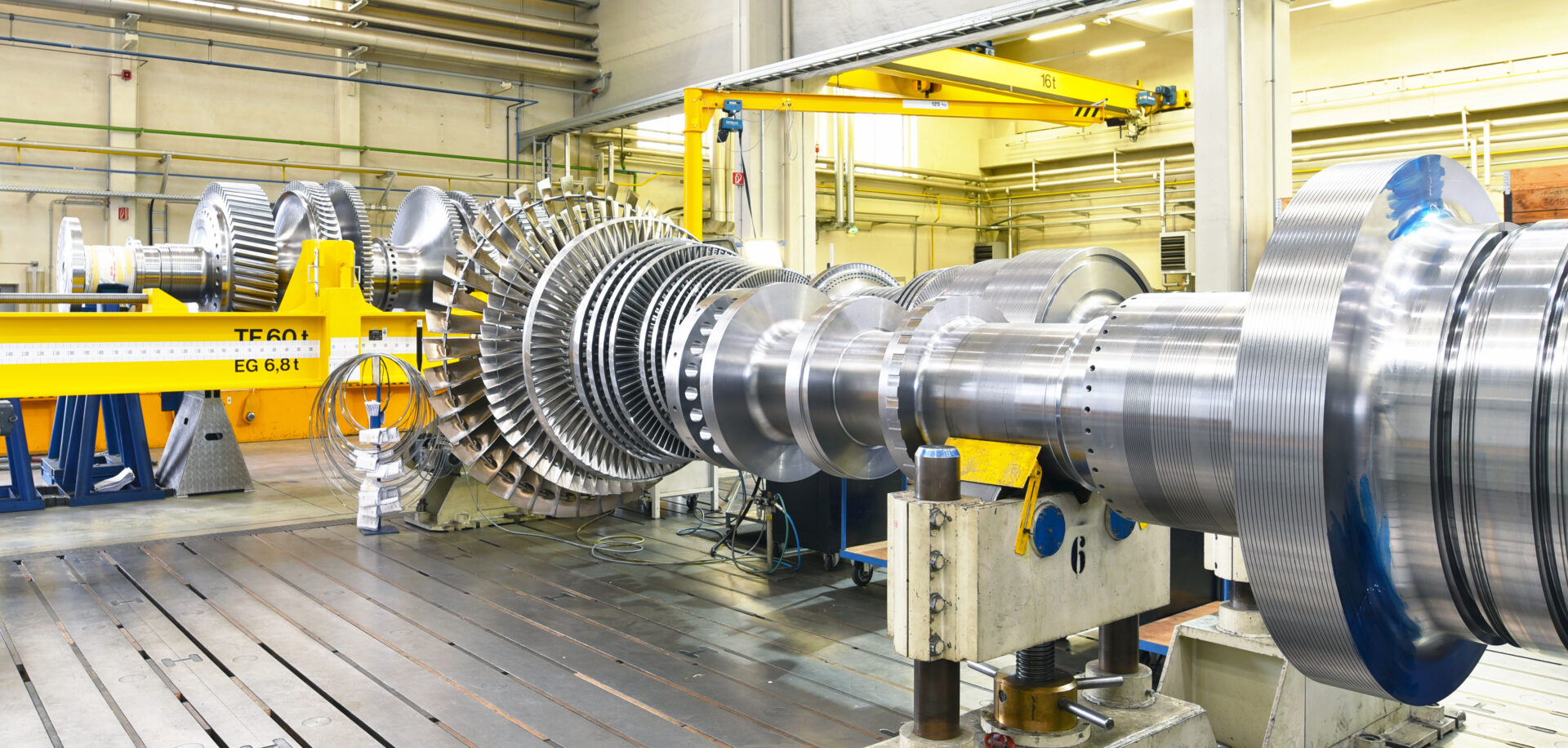
Power Generation Gas Turbines:
Common Components:
Aero Derivative Turbines:
Various Industrial Applications
Common Components:
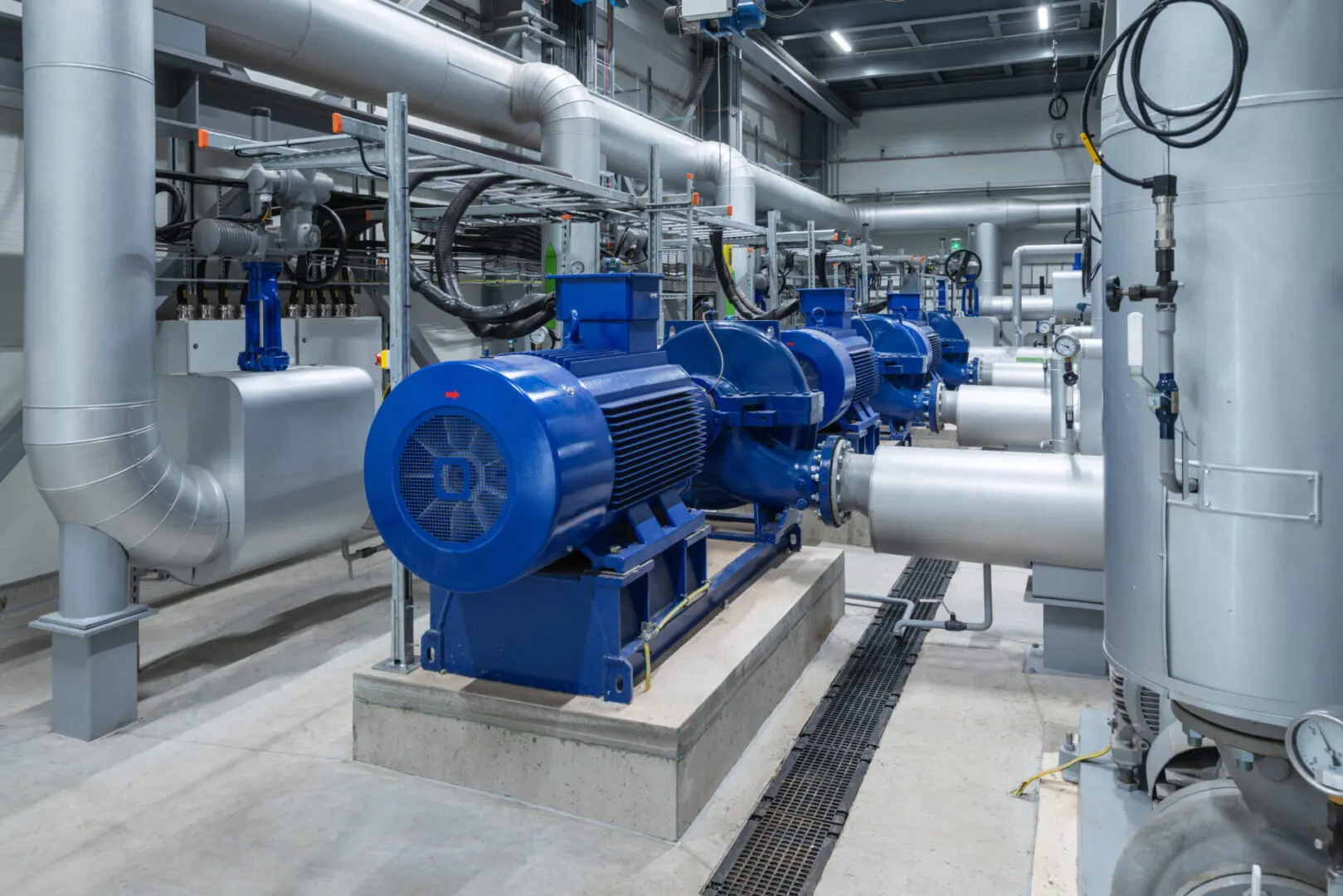
Thermal Spray
Coating Processes
Thermal spray coating is a terminology used to describe a group of coating processes in which melted materials are sprayed onto a part. The coating materials are melted and conveyed to the target surface by means of a combustion flame, plasma flame, or electric wire arc.
Coating Applications:
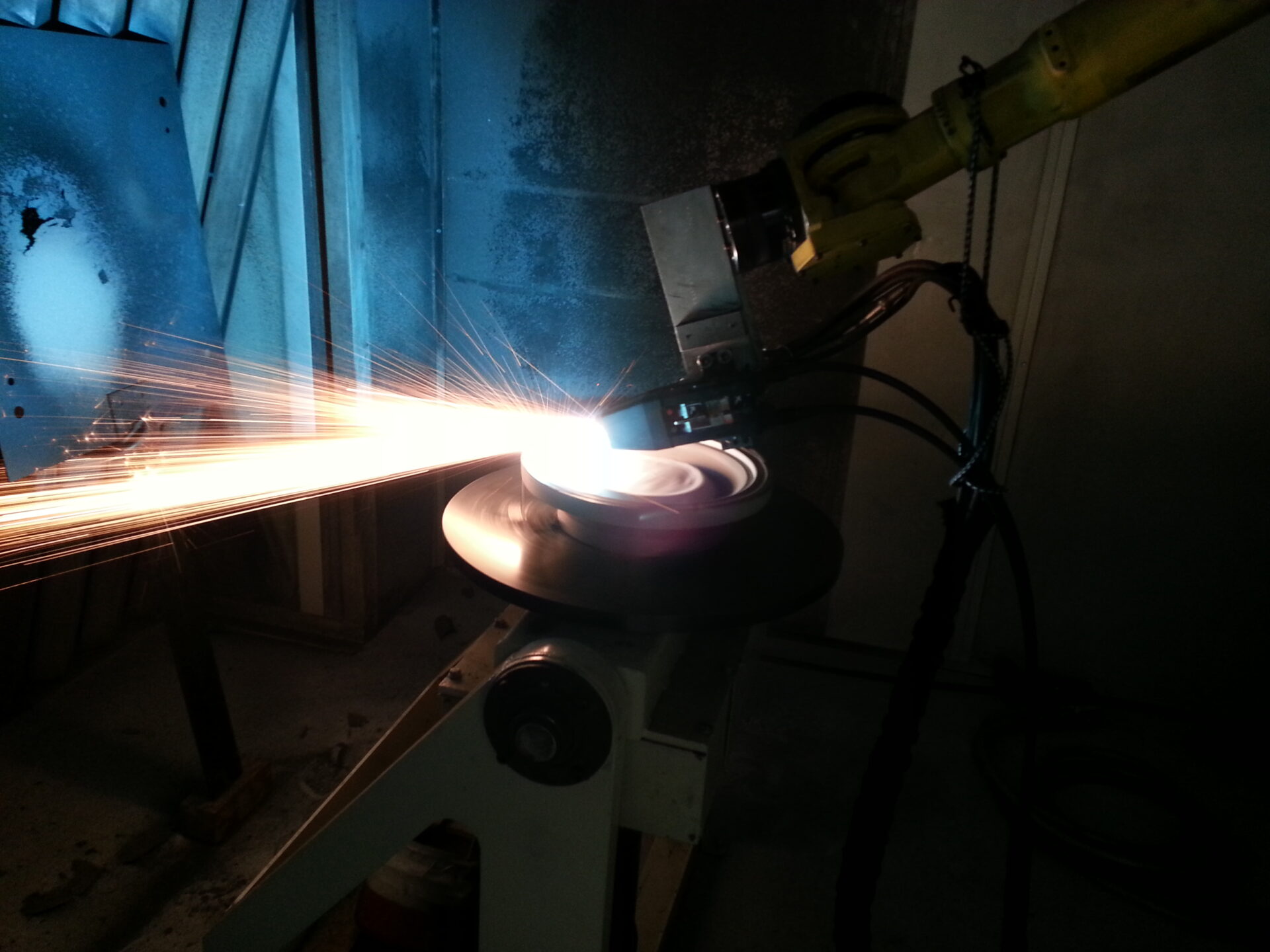
Wire Arc Spray
In the wire arc spray process two metallic wires are fed into the coating gun. The two wires meet at the tip of the gun where they melt as a result of an electric arc created between the two wires. Air injected directly behind the arc breaks up the molten metal and propels it out of the gun. The wire is fed into the gun in a continuous manner resulting in a steady stream of molten droplets exiting the gun.
The wire arc spray process can only apply metallic materials that can be formed into a wire. The most common application for wire arc spraying is the restoration of dimensions like internal and external diameters. The wire arc spray process is the most cost effective coating process.
Common Wire Arc Coatings
Plasma Spray
At the heart of the plasma spray process is the plasma gun. A continuous electrical arc is created inside the gun between the nozzle and the electrode and serves to heat the gasses passing through the gun resulting in a hot plume of gas exiting the nozzle. Powdered metal or ceramic materials are fed into the hot plasma plume. In the plume the coating materials are melted and propelled outward by the velocity of the plasma gasses. Nitrogen, Argon, and a small amount of Hydrogen (10%) are used as the plasma gasses. The plasma spray process is not a combustion process. The heat energy for the process comes only from an electrical power supply.
The major benefit of the plasma spray coating process is the ability to create a coating from almost any material that can be made into a powder. Typical plasma spray coatings are both metals and ceramics.
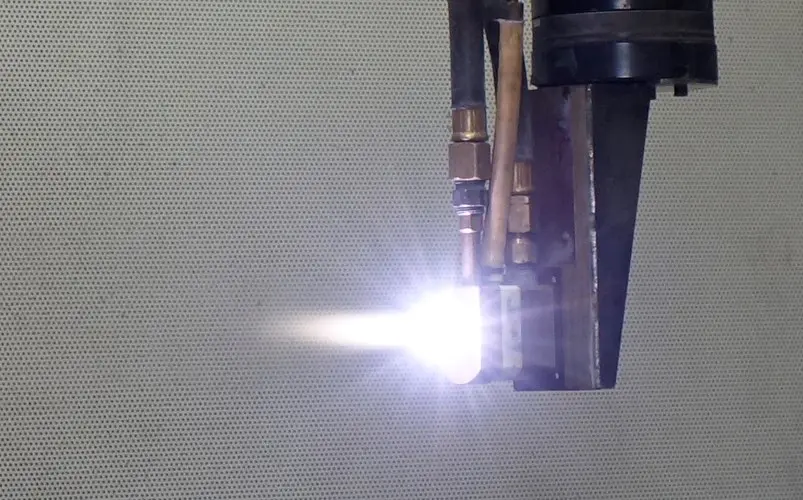
Common Plasma Coatings
Metals:
Metals:
Abradable:
Ceramics:
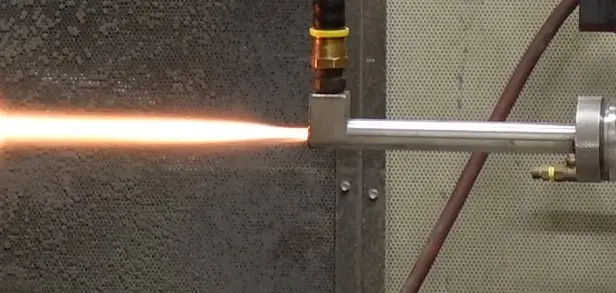
HVOF (High Velocity Oxy Fuel) Coating Process (Jet-Kote)
The HVOF coating process is a combustion process. Combustion of the process gasses, Hydrogen and Oxygen, takes place inside the water cooled HVOF coating gun. Metal powder is conveyed into the center of the flame through the rear of the gun. The metal powder is heated and accelerated out of the gun at very high speed. This results in a very dense coating with exceptionally high bond strength. The HVOF process is only able to apply metal material due to the natural limit of its flame temperature. However, due to the high quality of the deposited coating these coatings are desired for many demanding applications.
HP-HVOF (High Pressure High Velocity Oxy Fuel) Coating Process (JP5000)
The HP-HVOF coating process is very similar to the HVOF process. The main difference is that in the HP-HVOF coating process the fuel is kerosene instead of Hydrogen. Oxygen is used similarly as in the HVOF coating process. The most significant difference between the two processes is that in the HP-HVOF process the speed of the molten metal particles is even higher and the gun is larger. As a result more coating material can be applied even faster and with higher bond strength. As with the standard HVOF process the HP-HVOF process can only apply metal coating materials.
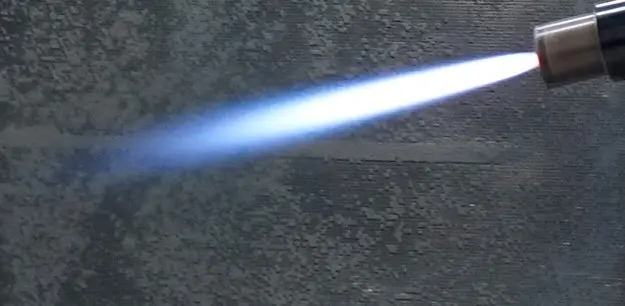